Since 1980, CycleSafe, Inc. has continued to innovate and raise the bar for secure bike parking products. We offer a complete line of bicycle storage solutions that are proudly Made in America and sold around the world.
Our company is best known for pioneering the modern bike locker, which was our first patent in 1976. In fact, we are the only bicycle locker company to utilize SMC, a sheet molding composite with the strength of structural steel that is impervious to rust, dents, and extreme weather conditions.
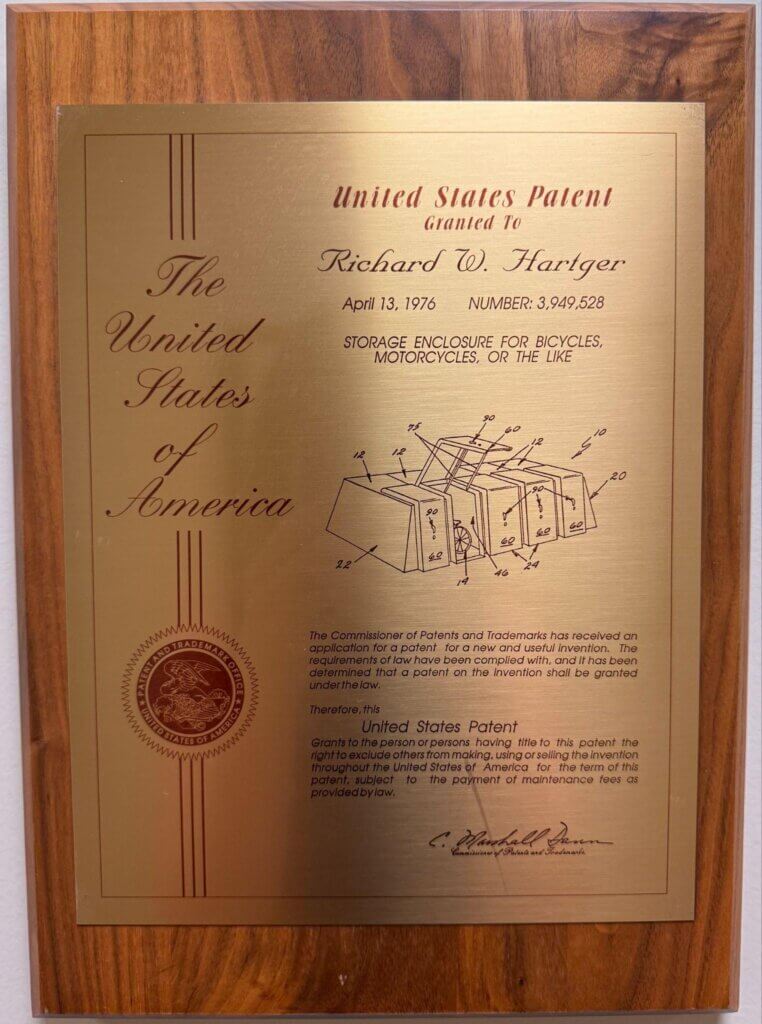
“Our differentiation from anybody else on the market is that we have extreme lifetime goals for our products,” says Hannah Hartger, CycleSafe’s Vice President. “We still have a product that is from our first manufacturing run on the street right now, being used 45 years later.”
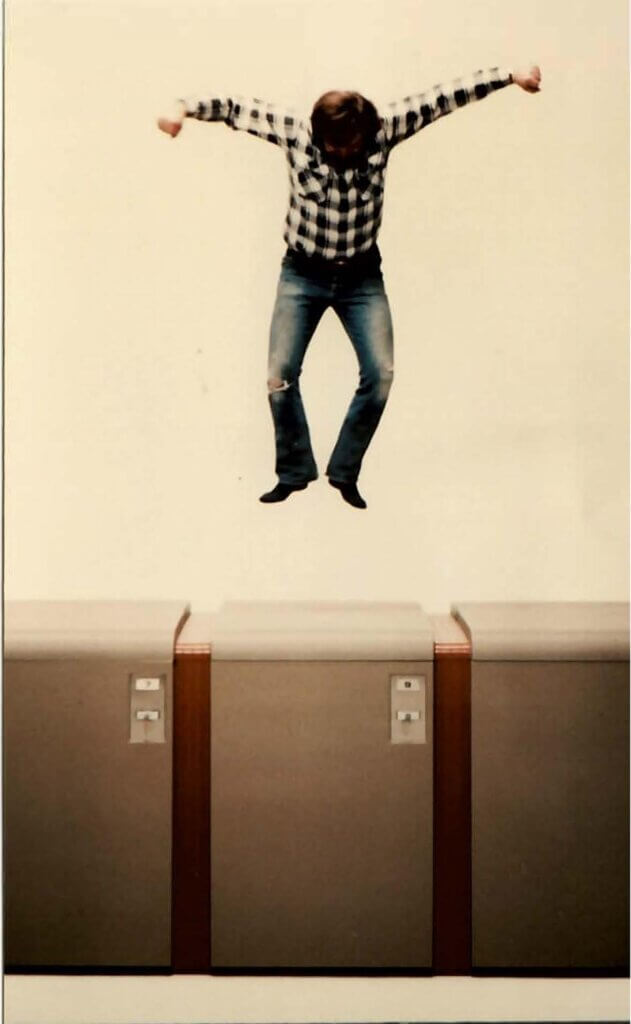
Leader in Bicycle Storage Solutions
Our products are built to last with durability, portability, and security in mind. Through the decades, we have continued to innovate and expand into new products and markets.
- Temporary, short-term solutions with contemporary or classic bike rack designs
- Fully enclosed and secure bicycle locker to encourage long-term commuters
- Space-saving vertical bike storage
- Hi-Density Racks
- WallRacks
- Weather-protected bicycle shelters
Our ProPark Bike Locker system remains our number one product line, but we continue to develop new bike parking solutions, blending the cutting-edge technology of our roots with today’s smart bike locker. The modular ProPark Bike Locker is available as an individual bicycle locker or a locker bank. A locker bank has expandable capacity for anywhere from four to fifty-six bikes and has different lock options, from a standard t-handle keyed solution to app-accessible technology.
“The most unique trait of our lockers is that they are composed of five main pieces that fit together like Legos,” Hannah says. “This allows easy locker expansion, swapping of damaged parts instead of replacement, and a seamless bank design. It’s a design that continues to be ahead of its time.”
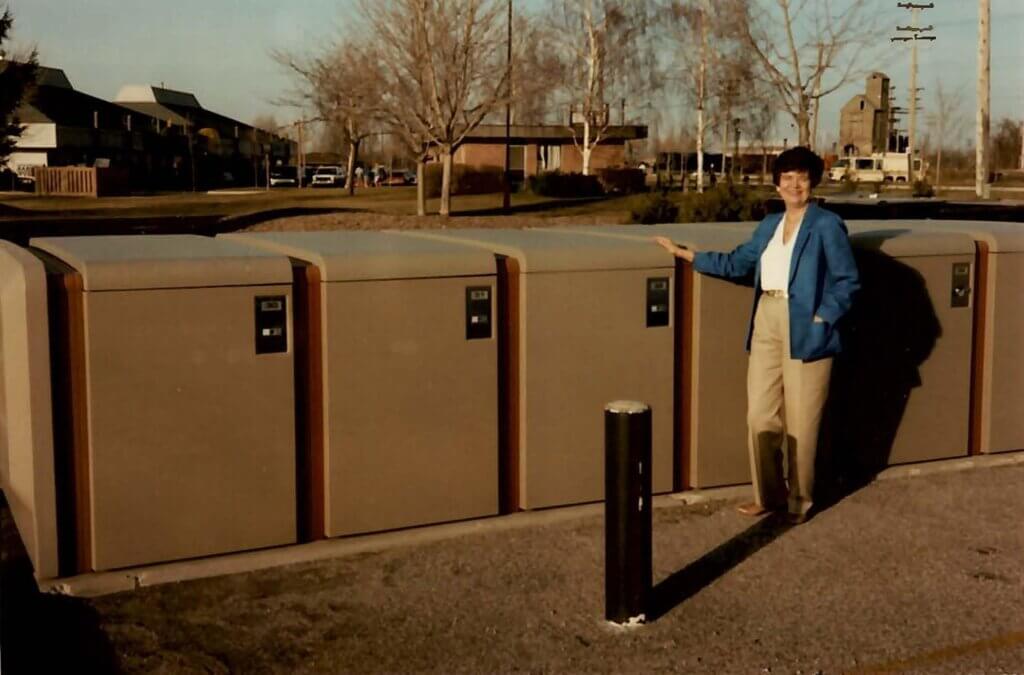
Continuous Improvement
In design development during the early years, 13 different families of material were tested before picking fiberglass SMC as our main material for the bike lockers. During testing, we evaluated the performance, quality, durability, and overall value to select the best material available.
“We design our products to last, with almost no end of useful life. We’ve gotten very good at solving problems before they even occur on the final product end. We made our decision to utilize fiberglass SMC after having all the facts, and the lifespan of our products speaks to that diligent work.” Hannah says.
One of the most significant areas of innovation has been the end panels of the ProPark Locker. This essential component has evolved through multiple iterations to enhance both strength and longevity.
The first design, created in the 1970s and in production until the mid-2000s, featured a tic-tac-toe pattern. Constructed initially from spray-up fiberglass, these early panels required six hours of production per side and introduced the patterned surface to increase structural rigidity.
As the product line advanced, the focus shifted toward modernization and efficiency. The goal was not just to continue to create a visually appealing design but to select a material and manufacturing process that could withstand real-world physical demands and maintain cost-effectiveness for our customers.
Beyond structural improvements, we also prioritized coating and paint technology to extend product life and enhance resistance to wear and tear. Every end panel is coated with a 2-part polyurethane solution, ensuring long-term durability and cleanability.
As we continued to evolve, modernization and efficiency became our key priorities. The end panels of today are enhanced with logos and branding, as well as notched in recessed areas to accommodate printed graphics and standard ad panels or wayfinding materials or maps for transit markets. To expand our advertising capabilities, our most recent iteration is designed to support digital screens, allowing for special product messaging and locker-related advertisements.
With these structural and branding improvements, we have prioritized technological integration. Recognizing the growing demand for e-bike charging solutions, the latest end-panel designs now include a GFI outlet inside the door (within a breaker box for safety). These modular panels are engineered to allow daisy-chaining of GFI outlets, ensuring streamlined power access across locker banks.
A key advantage of this approach is that modern parts remain compatible with legacy lockers, allowing for cost-effective retrofitting without the need for complete replacement.
With these advancements in design, materials, and electrical integration, we continue to push the boundaries of durability and innovation, ensuring that our lockers not only last for decades but also evolve alongside emerging technology and user needs.
We make sure that every product meets the highest standards of quality and resilience. These efforts allow our lockers to endure for decades, reinforcing our commitment to sustainability and innovation that our customers have come to expect from CycleSafe.
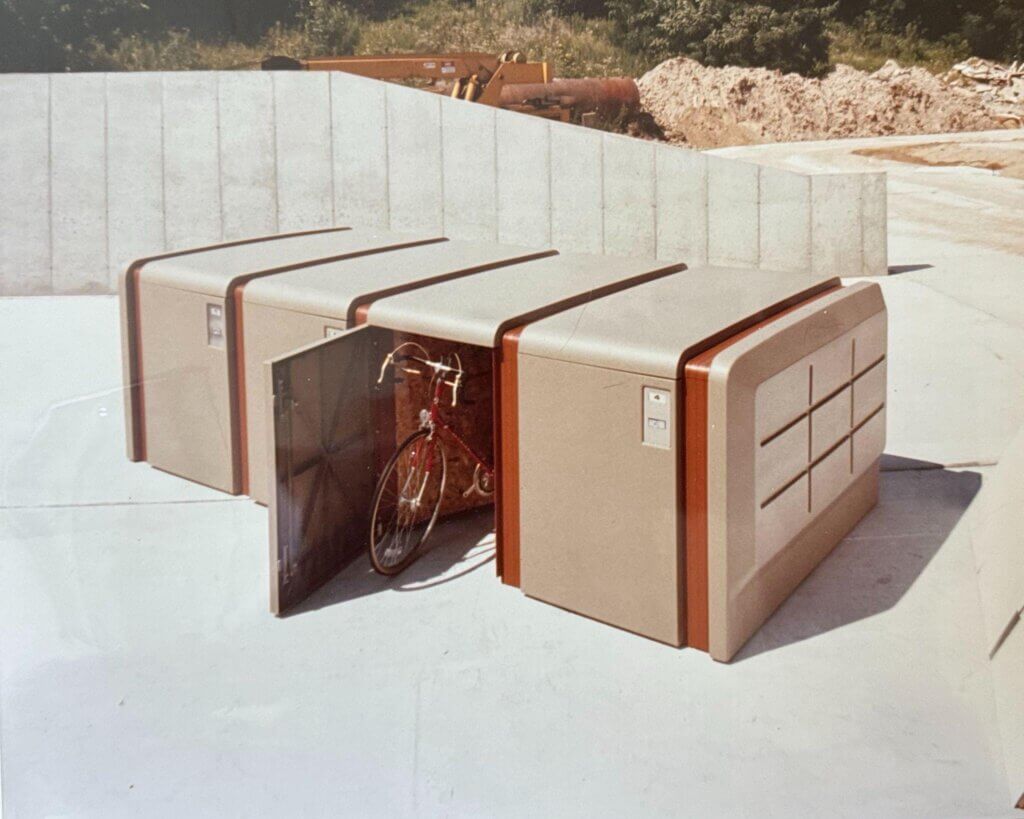
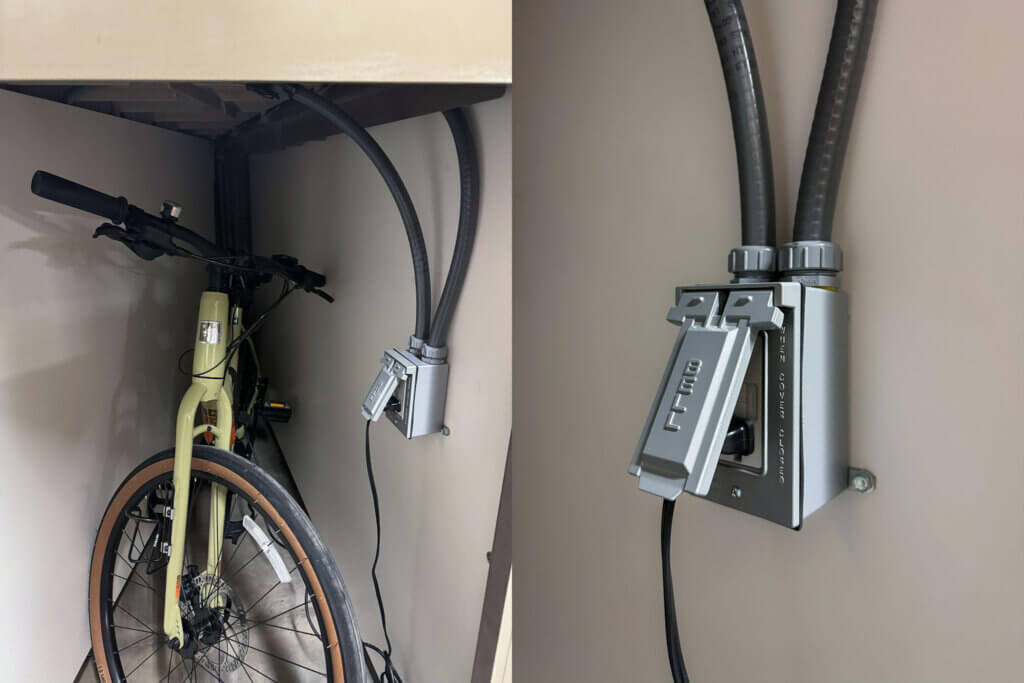
Innovation Leads to New Markets, Technology
CycleSafe serves communities in all types of markets, from corporate to municipal, education to healthcare, mass transit to multi-family units, and shopping centers to sports arenas. We offer bike parking and storage solutions that address code requirements and sustainable transportation initiatives.
Many municipalities are adopting bike parking regulations as a part of their city’s building code requirements, depending on the application, long-term, short term or a combination of both might be required. See our quick guide on bicycle parking regulations for US & Canadian cities. Don’t see your city listed? Let us know!
“For example, the rise in adaptation of e-bikes for micro-mobility in cities has brought a lot of attention to the topic of parking since the devastation of an e-bike fire can be significant. New York City has gone back and forth on banning the storage of e-bikes in high-rise residential complexes. Our ProPark bike lockers with added GFI outlets offer a safe way to store e-bikes while they charge, outside of the building, and in a locker made of self-extinguishing material.”
We developed the first patented bike storage locker and continue to innovate alongside technology to provide solutions that can easily be taken into the next few decades.
“The modularity of our lockers is a key design piece when we talk about retrofitting existing lockers with new technology. Lockers manufactured back in the 80’s and 90’s can be updated to be smart bike lockers, with app-accessible locks or keypad/RFID technology. When the next decade brings new technology around, we’re ready for it with easy, cost-effective solutions for our customers.” Hannah says.
Made in West Michigan
CycleSafe works with vendors and manufacturers in the Midwest, primarily in West Michigan and close to our company headquarters in Grand Rapids. Manufacturing occurs in Spring Lake, Muskegon, and Grand Haven, and we have a warehouse in Holland. The region is known for its furniture manufacturing roots and historical giants such as Herman Miller and car manufacturing suppliers with its proximity to Detroit.
“The area has a history of being a vibrant small-business community, and we have taken advantage of top-tier vendors from those industries. There’s a high bar set when working in the automotive supply chain or when supplying parts to one of the many legacy-level furniture manufacturers. We’re really lucky to have access to such high-quality partners – some of which we’ve worked with for over 25 years.
“We are 100 percent Buy America certified,” Hannah says. “Everything is both sourced and assembled here.” Being Buy America certified elevates CycleSafe from our competitors, improving both the quality of the product and the communities where our products are made.
“I always talk about how proud it makes me to have our products installed in communities all across the world, especially being such a small company,” Hannah says. “The impact we have on those that use our products is great; it’s a guaranteed ride home later. The fact that the product also supports local West Michigan jobs, to me, is the greatest impact of all.”